Dynamic Propeller Balancing
at Sensenich Propeller Service, Inc.,
Lancaster, PA
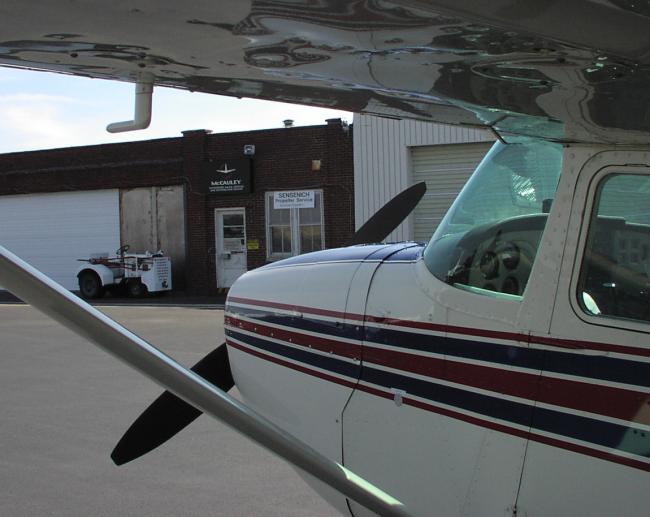
Arrived alive at the Sensenich Propeller Service field
office
Why Balance?
Our recent Annual Inspection afforded us with an opportunity to overhaul the 172's propeller. While we thought that the airplane never had any problems with engine and propeller- induced vibration, the first flight with the new propeller was like night and day. Of course, no piston powerplant will ever be as smooth as a turbine, and the tolerances on this 1400 hour Lycoming O-360 aren't exactly tight anymore, but we noticed a significant improvement.
Still, based on my experience with another aircraft, I figured I'd try to get the propeller dynamically balanced in an effort to document the vibration characteristics of the engine/propeller combination.
If the propeller turned out to be perfectly balanced (pretty unlikely, I thought, even if it was freshly overhauled), the dynamic balancing process would produce data to let me KNOW that it was. After all, you can't always use the "on-board instrumentation" such as shock-mounted panel instruments, the mag compass, or an approach plate attached to a yoke clip to figure out whether you have excessively high vibration, though I will admit that in a joe-sixpack kind of way, they're pretty reasonable indicators.
VFR to
LNS
Due to the fact that the airplane has spent more time in the shop than out for the last several months, my instrument currency lapsed, and I didn't have an opportunity to fly with a safety pilot, so I had to fly out to LNS VFR. That turned out to be a non-issue, because when I originally scheduled the balance with Priscilla at Sensenich, she noted that all work is done on the ramp, and they'd need good weather to do it anyway.
After a string of cancellations due to weather and work, I arrived one beautifully sunny early spring day in March to the humble field offices of Sensenich Propeller Service. I found A&P Mark working on a Yak with an obvious look of stress on his face. Turns out he had been overbooked and the Yak's radial engine and huge propeller just weren't cooperating. I asked how much more time he'd be, and he suggested about a half hour. I figured I'd take the time to taxi over to Airways, Inc. to pick up some fuel, check out the pilot shop, and take a walk around the Cirrus service center.
Upon my return 30 minutes later, the Yak was no where to be found, and Mark was ready to get started.
The Equipment and
Process
Years ago when I had another aircraft's propeller balanced the balancing equipment was huge. Its face was covered with a few dials, buttons, and an analog meter that was reminescent of something I'd find on an old school voltmeter. It was portable only in the sense that it would fit on the top of a dolly. It couldn't be brought inside the airplane, so one technician (or the owner/pilot) would run up the engine based on hand signals (or radio) from another technician, who remained outside with the gear to interpret the instrumentation.
Of course, times have changed, and the process of electronics miniaturization has produced the current state of the art in propeller balancing control units. The Chadwick unit measures a mere 7 x 9 x 1.5 inches, but at probably ten pounds it feels like it's filled with lead. The screen uses a membrane keypad for input and LCD screen for output.
Before we got started, I told Mark about my experience with the process, but that I couldn't remember the units or the range of acceptable values used. He told me that the vibration levels measured by the single accelerometer are in inches per second (IPS) and that a typical range of values is anywhere from 0.04 on the low side to 0.14 on the high side.
I then asked about the numbers he was able to get out of the Yak he'd just finished. With a weary smile on his face he told me that it was one of the more difficult balance jobs he'd done in a while, but that it was pretty typical for a radial engine -- they're simply more difficult to balance given the vibration characteristics inherent to that engine type. After an hour+ of fidding with various weight combinations, the best he could muster was 0.14 IPS.
Hands
On
I then offered to grab a screwdriver to help him remove the top half of the cowling in order to gain access to the top case bolts on which the accelerometer is typically mounted, but he quickly pointed out that would not be necessary. Evidentally the sensor mount is designed differently to facilitiate measurements with the cowling installed, but I'm sure the large openings in the front of our modified 172's cowling didn't hurt either.
I then watched as he mounted the optical tachometer sensor on the top of the cowling about 6 inches aft of the propeller blades. Good old-fashioned duct tape was used to secure it and the associated cabling, which draped down over the cowling and toward the pilot-side door and into the cockpit so he could watch over the instrumentation and runup the engine all by himself.
He then used a simple wooden stick to produce a straight line from the optical sensor to the propeller, which would indicate where to affix a small piece of reflective tape on the back of one of the propeller blades. The flat black paint on the back of the blades does its job -- a little too well, in fact, hence the need for the relfective tape.
Clear!
Indicated Vs. Actual RPM Data | |
Indicated RPM Mechanical Tach |
Actual RPM Optical Tach |
800 | 900 |
1500 | 1575 |
2000 | 2055 |
2500 | 2580 |
Full Throttle (Static) | |
2550 | 2630 |
After Mark was finished consuming the world's supply of duct tape, he brought the control head into the airplane and I hopped in on the right side to watch his work.
The process was pretty simple. We started a short warmup period at 800 RPM, and I began recording differences between the build-in tachometer and the RPM display on the Chadwick control head. The results, shown in the table, are quite telling.
The results are also pretty typical. Our mechanical tachometer read about 80 RPM low on average. I had wondered why our static RPM had appeared to drop from precisely 2700 to a touch over 2600 since the propeller and governor overhaul. Now I know why.
It now appears that Sensenich was right and the mechanic who tweaked the original governor to turn over at 2700 indicated was wrong. In fact, in the original configuration, we were actually slightly over redline at 2780 RPM. This isn't enough to cause any engine damage, particularly on a normally-aspirated engine that in slightly different forms is rated to produce far more than 180HP, but redline is set for a reason, and we don't want to exceed it under normal circumstances.
Smoooooooth
The biggest surprise of the day came when running the engine at two typical cruise RPM settings of 2300 and 2400. Mark turned the face of the balancing control head toward me so I could more clearly see the vibration analysis display. It read 0.04 IPS. There was little chance that we could get better than that, so Mark proclaimed victory and remarked ""She's pretty well perfect. No weights needed."
So, it turns out that Sensenich managed to perfectly balance the prop during the overhaul and precisely adjust the propeller governor RPM. There was nothing left for us to do except fly this thing!
Shutdown and
Paperwork
After we shutdown, Mark removed the cabling and sensors from the aircraft and called in to the main office to tell them the results. No sooner than I made a lighthearted comment about requesting a discount for helping to get him back on schedule, Mark told me that the office said it would only be $118 with tax for today, down from the original fee of $225. Thank you Sensenich!
I should point out that if you take your airplane to SPS and, in the unlikely event they find your propeller as perfectly balanced as ours, I can't guarantee SPS will give you the same discount. I don't know if it's an official policy or a special case, but we did give them other business recently, so that may have factored into the equation.
Since my mechanic still had the aircraft logbooks, Mark quickly accommodated my request to put the log entry on a sticker. The invoice arrived from the main office via courier about 15 minutes later and I was soon on my way down alpha taxiway taxiing to the active for departure.