Doug's APRS Aircraft Tracking Project
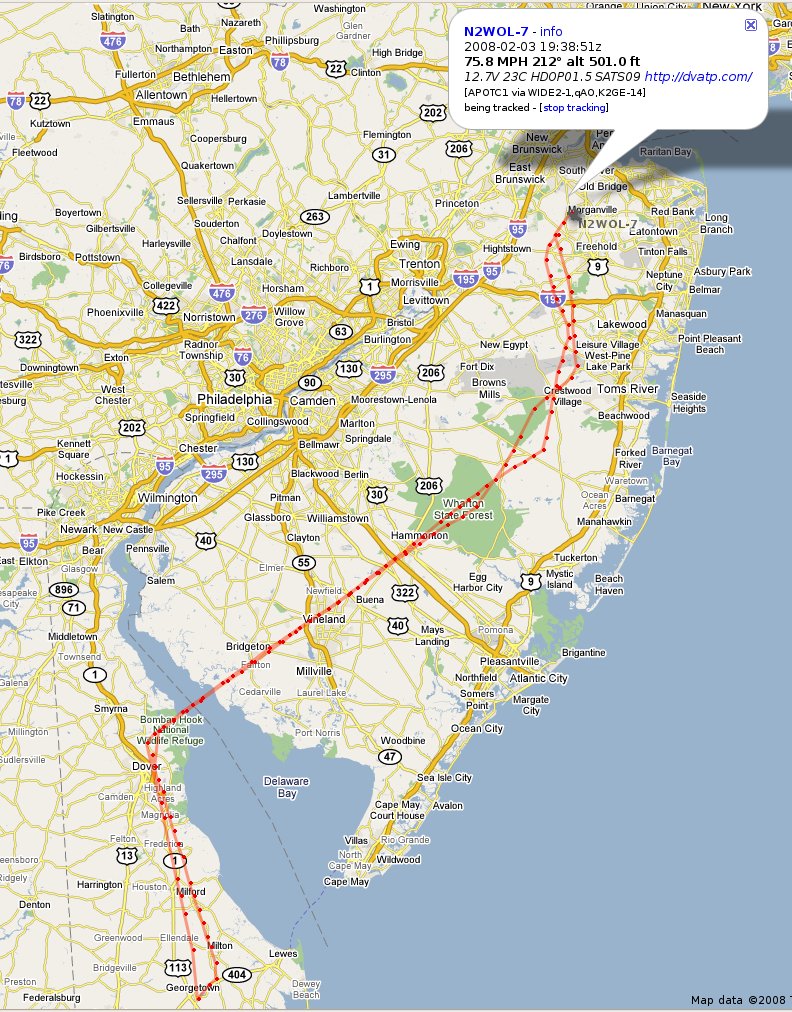
An experiment in aircraft tracking using the Automatic Position Reporting System
(APRS).
This is the first track obtained on an IFR flight from Old Bridge, NJ (3N6)
to Georgetown, DE (GED)
on Sunday, February 3, 2008. The variations in course near the top of the track
are due to vectoring
by McGuire approach and the dogleg on the southern part of the route was requested
to minimize
flight over (very) cold water south of New Jersey. Map courtesy of aprs.fi.
Introduction
This article explains how I built a device called an "APRS Tracker" to broadcast my aircraft's GPS-derived position, speed, and altitude via the Amateur Radio Service (ARS) Automatic Position Reporting System (APRS) radio network. The tracker consists of a GPS receiver, a tiny embedded computer, and a radio transceiver and antenna tuned to operate on the national APRS frequency located in frequency spectrum allocated to the Amateur Radio Service.
While browsing the net during holiday break late in 2007 I happened upon an article that described how a fellow Amateur Radio Operator attached a telemetry package to a balloon that reached over 106000 feet (!) It used an APRS tracker to report its position, the data from which was captured and then plotted using Google Earth. This wasn't the first such experiment I'd read about, but something about it piqued my interest so I set about to research what it would take to produce a tracker for my (admittedly far more mundane) operations as a full-size aircraft pilot.
What is Amateur Radio?
Since this article involves the use of an Amateur Radio transmitter, I can't write this article without an appropriate introduction to Amateur Radio. If you already know about Amateur Radio, feel free to skip ahead.
The FCC officially recognizes the Amateur Radio Service as a "radiocommunication service for the purpose of self-training, intercommunication and technical investigations carried out by amateurs, that is, duly authorized persons interested in radio technique solely with a personal aim and without pecuniary interest". To transmit on the vast amount of radio spectrum assigned to the Amateur Service, a person must take (and pass!) a knowledge exam and receive license credentials from the FCC. All transmissions from an amateur radio station must be identified in accordance with FCC Part 97.
There are three basic license classes: Technician, General, and Extra. Most people are Technicians. With a few exceptions, Technicians are largely restricted to VHF and higher frequencies, while General and Extra classes can operate on frequencies below VHF (so-called High Frequency or HF bands) to facilitate worldwide communications. There are a ton of cool things to do on HF, but I have always found plenty of practical things to do on VHF and UHF frequencies.
Until recently, obtaining full privileges in amateur radio required a demonstrated ability to copy morse code (otherwise known as Continuous Wave or CW). In 2006 the FCC eliminated this requirement so it's now easier than ever to obtain an amateur radio license. Of course, if you ever intend to use morse code in practice you'll need to learn it anyway, but it will be your option.
In the last 20 years the wide scale deployment of the Internet and cell phones have reduced the novelty of being able to communicate wirelessly, but Amateur Radio continues to fulfill its charter as a means of last resort communications in the event of civil emergency. Amateur Radio Operators were recently praised in California for their help during the wildfires, and in the aftermath of Hurricane Katrina when all the fancy cell phones were rendered useless by the destruction of the commercial communications networks.
There is so much to do in Amateur Radio -- from basic communications on HF, VHF, and UHF frequencies to digital modes that work whether your ISP is down or not -- that I invite you to become an Amateur Radio Operator and build one of these trackers for use in your own aircraft. If you're willing to invest a bit of money and time, I think you'll learn a lot and come away richer for the experience.
Major Component List
This is a list of the major components I used to build my tracker. This is not an all-inclusive list of materials nor does it represent the only parts that may be used to build a tracker. There are a number of ways to approach this project and the equipment I used might not be appropriate for your application.
Surplus Military Ammunition Can Source: Various ($10) I bought these years ago from a local sporting goods store but they no longer carry them. I did a quick Google search and found several vendors that carry them. Take your pick. Of the two sizes readily available, I used the larger of the two because I knew I'd have to find room for a relatively large handheld transceiver and tracker. |
Open Tracker 1+ (Assembled) Source: Argent Data ($46) This is a 1200 baud radio modem connected to a microcontroller that can interpret the data strings sent out by a GPS receiver, convert the information into an APRS packet and transmit it using Audio Frequency Shift Keying (AFSK) modulation. This comes in both kit and assembled form. Considering the scope of the project I felt my time was better spent integrating and testing the components rather than building up the kit from scratch so I bought the assembled version. |
Garmin GPS 18 OEM (PC Version) Source: Garmin Online Store The GPS 18 is known for its accuracy, quick acquisition times, sensitive receiver, and an ability to work at very high altitudes. It comes in three versions -- LVC, PC, and USB. The best choice for the OpenTracker is the LVC version because the OpenTracker supplies the required 5 volts DC @ 60 milliamps to drive the GPS, but I wanted to use the unit outside the scope of the APRS project so I bought the PC version. Incidentally, if you are considering buying a GPS 18 to serve as the time source for a Stratum 0 NTP server, you'll need the PPS signal that is only provided by the LVC version. Neither the PC nor the USB version will work in that application. |
2 meter Amateur Band Transceiver Various ($100-$200) I decided to use a retired handheld transceiver (HT) I had purchased many years ago (a Kenwood KT-78A). There are, of course, inexpensive 2 Meter HTs on the market (new and used), so if you don't have one you can probably pick one up for $100. There are also integrated tracker / transmitter solutions available but I avoided them because I felt blind transmissions on a busy APRS frequency, particularly when airborne, would be highly inappropriate. Make sure your airborne tracker utilizes a transmitter AND receiver so it doesn't abuse the service. |
Maldol / Comet AX-75 1/2 Wave 2 Meter Antenna Source: Ham Radio Outlet ($55) Ask any seasoned Amateur Radio operator and they'll tell you that no amount of power will make up for a bad antenna, so it's very important to use the right antenna for the task. In this case, that's a naturally resonant 1/2 wave antenna. At 30 inches in length the Maldol / Comet AX-75 is a bit unwieldy, but essential for good performance with modest transmitter power and no ground plane to speak of. I bought the UHF (PL-259) version because I knew I would be using it with a UHF (SO-239) antenna mount. |
Antenna Mount (SO-239) and Feedline Source: Various ($15) This is a SO-239 connector attached to a short length of 50 ohm coax feedline. I made it out of spare parts, but if I were to do it again I'd just buy one of the Larsen assemblies that comes with an SO-239 and about 18" of coax because it's cheap. |
12V Sealed Lead Acid battery Source: Various ($30) A sealed lead acid, AGM type battery is essential to this project, as it will not spill if the box falls over or if it is intentionally installed on its side. These batteries are commonly used by Uninterruptible Power Supplies (UPSs) as well as commercial or residential emergency lighting and can be found both used and new for a reasonable cost. |
Single Pole Switch with LED indicator Radio Shack ($3) I used this for the master power switch and insisted on an LED indicator vs. an incandescent bulb in the interest of reducing power drain. Some of the smaller bulbs designed for automotive use can consume several watts(!) vs. about a 1/4 watt for the LED. |
Single Pole Rocker Switch Various ($3) I used this to allow quick switching between for switching profile. Radio Shack carries similar switches that actually match the master power switch, above, but for various reasons I wound up getting this from an online PC parts vendor. |
2 8x10 sheets of 1/4" latex foam rubber Tower Hobbies ($10) I bought sheets of 1/4" and 1/2" thickness, and wound up using the 1/4" stuff because it was not as bulky. |
2 feet of 1/2" aluminum angle Home Depot ($5) Comes in a four foot length. Easily cut with a hack saw, though I used a professional carborundum blade chop saw I borrowed from the company. |
6 inches of 1/8" x 1" wide steel bar Home Depot ($5) This is to hold the battery securely. Like the aluminum angle, this came only in a four foot length. This might take some time to cut through with a hack saw, but the chop saw made easy work of it. |
Two (2) 5" long 3/8" carriage bolts with lock washers
and wing nuts Home Depot ($5) More components for the battery hold down assembly. 3/8" bolts are overkill for this application but I couldn't find anything smaller that was 5" long. |
One (1) 4" round electrical box cover Home Depot ($3) Part of the assembly installed on the exterior of the enclosure used to wrap the unused GPS signal cable for transport. I call this assembly the "GPS cable winder". |
Two (2) 3/4" hollow aluminum round bar Home Depot ($3) These are used as standoffs for the GPS signal cable winder. These parts are from a steel winching cable crimp set. It was actually cheaper to buy the $5 set and toss the parts I didn't need rather than use hollow round bar stock. |
Cigarette lighter plug and receptacle Various ($10) This is used for charging the battery and to provide power to other devices unrelated to the tracker. |
Control Cable for Radio ArgentData ($10) In order to interface my Kenwood radio I ordered the appropriate cable from ArgentData because the price was right and I didn't want to waste time looking for another source. This cable is wired using what is apparently a de-facto industry standard color code. |
Power Cable for Radio ArgentData ($5) This was the only thing I goofed up on. Everyone seemed to indicate that the Kenwood took a 2.1mm power connector but when I received the parts they were too big. Further research revealed that there are several smaller connectors but I never did figure out exactly which one because I wound up cannibalizing the AC power adapter I originally bought for the radio to get what I needed. |
Design Considerations
My primary design goal was to produce a package suitable for airborne use in the Skyhawk in order to explore routing issues in the APRS network. Secondarily, I figured I'd use it in the car on occasion. This meant that the design had to be tolerant of wide swings in temperature, pressure, vibration, and it had to be compact enough to fit in the confined cockpit space.
Enclosure
I considered both plastic and metal enclosures to house the tracker. While I knew it would be much easier to work with a plastic box, I discounted the plastic enclosure because I read of a case online where the transmitter affected the tracker electronics. I figured a metal enclosure would serve as an effective shield to protect the sensitive electronics.
The obvious downside to the metal enclosure is that its heavier than the plastic variety, but the bulk of the package's weight is in the battery, so this mitigates any weight concerns specific to the enclosure.
Antenna
While researching the enclosure, I learned something new. HT antennas don't work (well) for trackers because they rely upon a ground plane to radiate properly. Normally the human operator serves as a lossy ground plane which explains why HTs work as well as they do in normal operation. However, put the HT down and give some electronics module (like a tracker) the ability to hit the PTT switch and you have no ground plane. This results in a mismatched antenna that will have a poor SWR and likely force a bulk of the RF energy to exit the radio on every cable OTHER than the antenna feedline. This can and has, in practice, caused trackers to glitch or reset.
The way around this, of course, is to use a naturally resonant 1/2 wavelength antenna that does not require a ground plane. The only downside is that 1/2 wavelength at 2 meters is a honkin' 39 inches. Fortunately, I happened to find a dual band (2M/70cm) mobile antenna that fit the bill -- the Maldol AX-75. The perk? It's only 30 inches high from base to tip. And while it's an expensive antenna for this application, I bought it knowing full well it could serve double duty as a general purpose mobile 2M/70cm antenna.
Tracker
I spent hours comparing the various trackers and Terminal Node Controllers (TNCs) on the market, but ultimately wound up buying the OpenTracker from Scott (N1VG, D/B/A Argent Data Systems) for a number of reasons:
- Scott's great support. He's one of those people that "gets it". I believe product support is at least as important as the product itself. Anyone who's dealt with a "John" or "Mary" with a strong Indian accent reading from a script to open a Dell support case knows what I'm talking about. Scott promptly and clearly answered my emails -- even on the weekend.
- The project is open source. Scott freely provides the schematic and the source code to the firmware that runs on the device so that if you're so inclined you can modify and recompile the source for yourself. Frankly, in spite of the fact that I do embedded programming for a living I have no intention of doing that, but it's nice to know I could do it if I were so inclined.
- It contains a receiver as well as a transmitter. Several of the other popular trackers including the otherwise innovative Byonics models lack a receiver and thus blindly transmit regardless of whether the frequency is in use. The OpenTracker supports software carrier detect and can be configured to wait for the channel to be quiet for a specified period before it transmits. This ensures the OpenTracker plays nice with others in busy APRS locations.
- The unit will transmit either a fixed position or a position derived from the GPS. Several devices that claim to be full-featured trackers can't be configured to operate without a GPS. What about usage with weather stations or other fixed locations?
- The OpenTracker accepts 6-28 volts DC. In other words, Scott has done his homework and chosen parts that can tolerate a wide voltage range. This is important when one considers that SLA and AGM batteries in particular have a higher no-load voltage than standard 12 volt batteries. In fact, I routinely measured 13.5 volts (unloaded) from one of my batteries while testing and this was conspicuously on the upper voltage limit of the Byonics devices. I'm not sure whether the Byonics units could have handled more, but that's not because I didn't ask. In fact, they didn't respond to my email.
- The device has on-board temperature and voltage sensors and can be provisioned to report the data in the APRS packet comment field.
GPS
I chose a GPS 18 OEM PC because I liked the fact that it came with the data cable already terminated in a DB-9 that I knew would be plug and play, but I also preferred that it came with a cigarette lighter plug and integral 5V voltage regulator so I wouldn't need to rig up something else when I connected it to a computer for firmware updates. The only downside to this solution is that the power connector is bulky. Fortunately, space wasn't a critical concern.
Electrical
The battery is a 12 Amp Hour 12V unit of the sealed lead acid (SLA) variety. Generally speaking SLA batteries can be oriented in any way except upside down. In fact, this battery came from a UPS and I have seen batteries similar to it installed on their side by design. Since I expected to utilize my tracker with the case (and thus the battery) both vertically and horizontally, this was an important design consideration.
The basic power budget was for a 200 ma draw at idle with peaks to up to 2 amps during transmit at high power (5 watts). The GPS requires 60 ma, the tracker current drain is not documented, but I imagine it to be on the order of 30 ma or less during transmit. The radio, on the other hand, being 15 year old technology as well as containing the transmitter -- is the obvious power hog of the bunch.
With an average transmit rate of once every two minutes I expect the battery to power the tracker for days. I don't expect to use it that long, but can you imagine how useful that would be if I crashed on a remote mountain top somewhere and it took people a day or more to figure out I was missing? (For the record, I always file IFR on long trips so that's probably an "impossible" scenario, but ya never know).
One of the most critical things you can do in any electrical design is properly fuse it. I reused some fuse holders provided with one of my mobile rigs and installed 5A fuses on both power and ground lines. I installed the fuses as close to the battery terminals to afford the internal wiring as much protection as possible. I blew one of the fuses during testing (in haste and, fortunately, without any sensitive electronics attached), so they are essential to the design.
I added a 12 volt cigarette lighter receptacle to the design and made it unswitched for two reasons:
- To make it possible to use the system as a power source that did not require the tracker electronics to be active.
- To allow charging of the tracker battery without opening the case.
Assembly
The best advice I can give to anyone building a tracker is to think things through before you buy anything and test each component separately to ensure it functions as expected before you integrate.
Enclosure
I used a combination of drill bits and Greenlee metal hole saws to cut the holes in the box as needed for ventilation and to fit the various switches and receptacles. I also bought a couple fine metal files to trim the holes as needed since some of the drilling techniques left very sharp edges and some of the switches had anti-rotation guides and retaining clips built into them and would not fit in a perfectly circular hole.
I originally planned to use a 120mm cooling fan to circulate air through the box so I could ensure the accuracy of the temperature reported by the tracker so I bought a couple nice metal fan grills. As I narrowed the focus of the project I decided to eliminate the fan but drill holes of various sizes in the ends of the enclosure and use the fan grill to dress things up. I think the result is quite nice looking as well as functional.
Normally I wouldn't have bothered to paint the enclosure (the original Olive Drab actually looked kinda neat). Unfortunately, it also looked suspiciously like a high caliber ammunition container. Considering I planned to take it to "sensitive" areas like my airport, I felt it would be best to paint the box to remove the military markings and thus make it look more like test equipment.
I used some Scotch Brite pads (synthetic steel wool) over all surfaces of the enclosure to roughen the paint and paid particular attention to the interior corners of the box where some rust had formed. I sprayed the entire box with some rust-ready primer I used successfully on an earlier project and then painted using some satin black Krylon.
Since I was doing this in the dead of winter and the solvents in the paint take DAYS to evaporate when it's below 40 degrees I pulled the car out of the garage, suspended the parts from the ceiling, painted the parts, and then strategically located a Kerosene heater below the parts to aid the drying process. Even with a couple light coats of paint and the heater doing its business the paint took over six hours to fully cure. I hate winter.
When it came time to figure out how to connect the coax feedline on the inside of the box to the antenna on the outside I tried to leverage parts from an old mobile mount I had in my parts bin. That failed because I couldn't get the connector to stop spinning whenever I'd try to install or remove the antenna. I tried again with a barrel connector thinking I could get the hex nuts tight enough...but I was wrong. I ultimately scrapped that idea and went with the chassis connector. Four screws and nuts very securely fastened the connector to the enclosure and now I can wrench on the antenna all I want.
Another interesting tidbit about the chassis connector. If you look closely at the pictures, you'll see the outside circumference of the connector has a notched appearance. That is critical to my application because I needed those to interlock with a right-angle adapter to keep the antenna vertical. The mobile mount parts I tried to use did not have that because they are designed to be used with a secure mounting base...that I wasn't using here.
GPS
I tested the GPS first, and I'm glad I did, as the unit took the better part of 15 minutes to lock. Without the status information provided by the Garmin configuration application I probably would have grown frustrated at the tracker or some other component when the unit didn't lock and start transmitting my position immediately.
It's quite common for GPS units manufactured elsewhere in the world to take some extra time to lock, since the GPS unit will use its almanac to listen for satellites it thinks should be overhead given the current time and the last known position. If I hadn't connected the Garmin configuration program to the GPS I would never have realized the last known position was in Taiwan.
My GPS came with the latest Garmin firmware (3.20) so I didn't have to upgrade it but the Garmin configuration application makes that a pretty painless operation.
The only snag I had was that I couldn't get the unit to talk to the serial port under Linux, so I had to do my initial configuration on the dark side (Windoze). Of course, I couldn't connect to it there either, initially, and I'm not sure why. I selected the proper model and used both Auto and Manual speed settings (the PC version supposedly defaults to 4800 baud and NMEA operation), but I had to try it "several" times before it connected successfully. I ran it for a few hours in the following days and it connected okay.
Tracker
I tested the tracker next and poured over the manual to investigate every setting. I advise anyone working with the device to do the same. Save Scott the email and RTFM. Everything you need to make it work is in there, though certain elements like profile switching may require a double-take. The OpenTracker is a surprisingly complex device for as simple a hardware design as it is, so you simply won't get around this.
The most important feature for my design was profile switching, which I planned to use to quickly convert the tracker from car to airplane use. In my design, Profile 1 depicts my tracker as a Car (symbol characters "/>") while Profile 2 depicts me as a small airplane (symbol characters "/'").
Profile switching is accomplished in my design through a SPST switch that pulls pin 4 of connector X1 (the "Radio" interface) to ground. In the profile settings dialog I checked the "Jumper" checkbox on both profiles to enable profile switching based on the state of Pin 4. In this context, "On" means a 0 or pulled to ground, thus in order to provision the tracker to switch to profile 2 when I flip the switch to "On", I configured the logic to "Switch to Profile 2 when" Jumper is ON. I located the profile switch under the enclosure's latch so it cannot be accidentally changed while the device is in operation.
For debugging purposes and to mark the time of the change, I configured the tracker to transmit when switching profiles.
Audio Levels
I set the Kenwood HT receive audio volume to half or "10". I used the OT configuration program to set the tracker's transmit audio at the middle of the allowable range. Lacking a deviation meter I used my 2 meter base station to conduct the subjective audio quality measurements suggested in the tracker manual and I wound up leaving the Transmit audio more or less in the middle of the range.
Wiring Harness
I used some spare 14 gauge stranded wire left over from another amateur radio project and consistently used Black for ground and Red for line. The fuse holders were also left over from the wiring provided with one of my mobile radios.
I was able to use common spade terminals obtained at Home Depot for all switch connections. All wire-to-wire connections were soldered and I applied heat shrink to all connections to eliminate any chance for a short circuit.
To eliminate the need to solder or crimp the DB-9 pins I bought a DB-9 (male) -> DB-9 (female) cable from ArgentData and cut it in half. The column "Wire Color" refers to the colors in this cable. I am not sure if this matches any wiring standard or even if you would receive the same color code if you ordered the same cable from Scott at this point. Moral? Make sure you ring out the cable and confirm the pinout.
Radio - Tracker Wiring Connections | |||
---|---|---|---|
Tracker Pin | Function | Wire Color | Connect To... |
1 | Audio Out | Black | Mic (Kenwood Cable White) |
2 | COR / Squelch Input | Brown | N/A (cut and heat shrink) |
3 | PTT Output | Red | PTT Output (Kenwood Cable Blue) |
4 | Counter / Xmit Now / Profile Input | Orange | Profile Switch (other side of switch is connected to ground, which is also pin 6) |
5 | Audio Input | Yellow | Radio Speaker (Kenwood Cable Red) |
6 | Ground | Green | Ground (Kenwood Cable Bare Shield) |
7 | Power Input (+12V) | Blue | 12V (switched) |
8 | PTT Input | Purple | N/A (cut and heat shrink) |
9 | ADC5 Input | Gray | N/A (cut and heat shrink) |
Testing and Operation
Tracker and GPS
During the debugging process I developed some opinions of the tracker and the GPS.
The OpenTracker performed to my expectations. The only thing I do not like about the OT design is the lack of discrete status indicators (LEDs). It sounds like such a trivial thing, but given that I cannot have a computer attached to the device when it's in operation and the GPS itself has no status indicators, the tracker's indicator LED(s) are the only way to figure out what is going on.
The problem with using a bi-color LED is that even in ideal lighting it is VERY hard to discern status at a glance, particularly when multiple events are occurring in quick succession. I expect to get around this by desoldering the bi-color LED and replacing it with a couple separate LEDs -- one green and one red -- both mounted to the exterior of the enclosure so I can see what's going on even when the enclosure is buttoned up.
One of the things I did while configuring the Tracker was calibrate the on-board temperature sensor. Mine consistently read three (3) degrees Celsius high so I put "-3" in the "Temp Adjust" field.
I read several accounts online that indicated the GPS 18 was more sensitive than most GPS receivers. I didn't find that to be true. Don't get me wrong -- I think it's a great unit -- but it's nothing special unless you're comparing it to the units of 5+ years ago that wouldn't lock unless they were outdoors. With the GPS 18, receipt of 5-6 satellites is common indoors, with 8-10 satellites more likely when in mobile operation with a clear view of the sky. The newer SiRF units are supposed to be fantastic, and if my friend's experience with the new TomTom navigator is any evidence (which pulls in 12 sats even indoors), that might be the better choice.
One of the first things I did after connecting the Garmin-proprietary configuration application to the GPS was to disable the Garmin-proprietary sentences as they would serve no purpose in this application.
Airborne Tracker Considerations
Like a cell phone network, the APRS network is designed primarily to serve ground-based trackers. Use of any improperly configured tracker while airborne can result in extensive disruption to the APRS network for the very simple reason that an airborne tracker can hear and be heard by potentially hundreds of ground stations. This causes two specific problems: the first is related to routing and the second involves the performance of the airborne tracker itself.
The optimal PATH value for a ground based tracker is "WIDE1-1,WIDE2-1". That means "route through a fill-in digi first, like someone's home station, and then through a single WIDE digi up on a hill somewhere". If I used that path while airborne I risked aggravating a lot of people because my packets would attempt to route through countless home stations. That, in turn, would lead to excessive transmissions on the RF network and duplicate packets sent to the APRS-IS internet servers via IGates. Scott and others on the OpenTracker mailing list suggested use of the path "WIDE2-1" for my airborne tracker so that is what I used for initial testing.
Because the airborne tracker can hear hundreds of stations it may perceive the frequency to be continuously busy. This means if the tracker is provisioned to wait until the frequency is clear before transmitting it may never actually transmit. For this reason I disabled (set to 0) the Quiet Time feature in the airplane profile (only). It may sound inappropriate to blindly transmit, but it's necessary at times.
The amateur radio mantra has always been "start at low power and work your way up" as to avoid unnecessary interference. This is especially important for airborne trackers due to their increased range. I started testing at the lowest power supported by my HT in this configuration -- 1 Watt.
The accepted minimum transmission interval for a mobile tracker is two (2) minutes. The smart beaconing feature adjusts the transmission interval in real time based on the course and speed of the tracker. While I configured the tracker to use smart beaconing on both car and airplane profile, the configurations are slightly different for a variety of reasons.
Data Mining Results
I used the awesome site aprs.fi in combination with Xastir to determine if my position reports were being received by a local IGate or digipeater.
Testing revealed that the unit is a better airborne tracker than a ground-based tracker and it's not hard to understand why. Even transmitting at 5 watts, handheld transceivers are very limited in range on the ground. This is particularly true if operated with an antenna inside of the vehicle because the vehicle's metal skin acts as an effective Faraday cage. If you've ever used an HT for voice communications, you already know this to be true.
The problem is exacerbated by the fact that data transmission requires full quieting for error free communications. The so-called "Picket Fencing" effect experienced while mobile is a mere annoyance to analog voice communications but it's deadly to digital modes because as the signal drops out, so do any bits transmitted at the same time. In AX-25 "connected" mode, the destination can detect the error via the Frame Check Sequence (FCS) and request a retransmission, but since APRS is a broadcast protocol defective packets are simply dropped. This can (and does) result in a decrease in range and high rate of packet loss while moving. If transmission occurs infrequently as it does in APRS operations, the loss of only two or three position reports can result in a wildly inaccurate track as the client software simply draws a straight line between the position reports.
For this reason, I advocate a more aggressive transmission interval when running low power from a mobile ground-based tracker to improve one's chances of communicating successfully. Naturally, however, as power output or elevation increases the frequency of transmission must decrease to prevent network saturation. If the tracker is stationary, of course, then the accepted transmission intervals for stationary targets applies (typically 5-30 minutes, depending on the purpose of the tracker). This kind of adaptive transmission rate is made possible in part through the use of smart beaconing.
While airborne various APRS data sites I visited noted a few errors in the packet stream, but the most often reported error related to the tracker "moving too quickly". I imagine this was the result of being heard by too many IGates and those IGates reporting too many packets to the APRS-IS servers within some set interval. In spite of this, the results speak for themselves. The tracker works quite well while airborne.
If you want to see what the raw APRS message data from my first flight with the tracker looked like, check this out.
Doing our part
You can build trackers to your heart's content, but ultimately the tracker is only useful if it can reach a digipeater or IGate. In other words, like cell phones, it's only as good as the network it's on. I discovered this first hand while testing the tracker at the home of my friend Todd (KB2GGS).
We noted that in spite of being on a pretty tall hill we were not able to hear any digipeaters and no IGates were within receiving range because neither my tracker's packets, nor those of Todd's newly configured tracker (based on Scott's OT2) were making it to the net. The solution? Todd decided to set up a receive-only IGate and help out coverage in that area. If you are getting your packets delivered to the net while in the vicinity of Routes 78 and 31 in Clinton, NJ, thank Todd. I'm sure bills of large denomination will be appreciated. :-)
Highlights
Revision 1
After several flights with the tracker I found one flaw in the design. I originally concluded the GPS cigarette lighter adapter would mate reasonably well with the receptacle I had on hand. Unfortunately the connection was anything but reliable and caused the GPS to intermittently turn off in mid-flight so I lost data on several flights before I determined the source of the problem.
The obvious solution was to hard-wire the power connections. My first idea was to cut off the stock DB-9 connector and wire up my own with power obtained from pin 4 of the tracker's GPS port, which can provide 5V @ 200 mA for this purpose. When I cut off the DB-9 I found black (ground) and red (power) wires but when I plugged in the cigarette lighter adapter I found no voltage there. This meant Garmin used the same cable throughout the assembly but did not connect the power wires going to the serial port to the output of the cigarette lighter adapter. This wasn't exactly a surprise but it meant I had to take more drastic measures to power the GPS from the tracker.
To make a long story short, I cut the entire Y cable off the GPS, wired in a DB-9 connector with the red (5V) and black (ground) wires from the GPS connected to pins 4 and 5 of the tracker's GPS port, respectively. I also pig tailed the power connections and terminated those wires with some gender-keyed spade connectors so I could power the device using the now orphaned cigarette lighter adapter while the GPS is connected to a computer for programming. Naturally, I used keyed connectors so they could never be connected with incorrect polarity. I'd like to think that Garmin built reverse voltage protection into the GPS design but I did not want to be one to find out they did not.
Revision 2
I decided to add a few features that were omitted from the original design:
External tracker status LEDs
One of the biggest problems with the original design had to do with the tracker's LED status indicator. First of all, my design put the tracker inside of the box, so it's no surprise that I had trouble figuring out the status of the device with the cover closed. Of course, I wound up opening the box as necessary but this was less than convenient with the box installed in the baggage compartment. And as I mentioned previously I found the bi-color LED difficult to read under ideal circumstances.
For these reasons I removed the bi-color LED and replaced it with separate red and green panel-mount 5mm LEDs mounted on the exterior of the box. The change is a notable improvement in the design because I can now tell at a glance what's going on with the system. The red LED flashes when there is an issue with the GPS or when the system is transmitting, and the green LED flashes once a second when a GPS position is received or when the tracker is decoding an APRS data packet. And of course they flash simultaneously when a position is received and decoded.
External voltage meter
Since this is a battery powered device I'm naturally concerned about the present state of the battery. I knew I should have installed a voltage meter in the original desgin but never did find the part I wanted at a reasonable price -- until now. I found the Murata Power Solutions DMS-20LCD-0 DC voltage meter via DigiKey's site to be ideal for this solution. This particular part provides a range of 6.5-18 volts, resolution down to one hundredth of a volt (.01V), samples the voltage 2.5 times a second (fast enough to catch the voltage drop due to transmitter load -- a good indication of the relative health of the battery), is self-powered (meaning its supply voltage is in the same range as the sampled voltage) and only draws a measily 2mA during normal operation. Best of all, the part was only $30 in single quantity.
Conclusion
The tracker I built is effective while airborne and not really usable while on the ground, but that's no big deal since I never intended to use it on the ground except during taxi in the airplane.
This is the project that got me back into Amateur Radio after a nearly ten year hiatus. Though tedious at times, I had more fun building the tracker than I thought I would. It reminded me of days of my youth I spent exploring and experimenting just for the fun of it. It cost an estimated $275 to build, not including the various parts I had on hand, and probably consumed about 25 hours of my time spread over several weeks. Not exactly an insignificant investment, but when things are this fun, who's counting?